Pour un fabricant de matières plastiques, le temps de cycle de moulage est probablement le critère de rendement plus important de tous. Le temps de cycle de moulage est le temps total nécessaire pour mouler une seule dose de plastique pendant tout le cycle pour en faire une pièce complète. Généralement, cela inclurait le temps à partir de l’injection de plastique dans le moule jusqu’au début de l’injection de plastique suivante. Le temps de cycle dépend du design du moule, de la configuration de la cavité (pièce) et du matériau devant être moulé. Le temps de cycle total comprend le temps nécessaire pour injecter le plastique dans le moule, refroidir le plastique, ouvrir le moule, éjecter la/les pièce(s) et refermer le moule. Le temps de refroidissement du matériau dépend des caractéristiques des conduites de refroidissement conçues dans le moule, et de l’épaisseur du matériau moulu (taille et géométrie de la pièce). Le type de matériau est également un facteur dans le temps de cycle.
Le temps de cycle de base (théorique) est élaboré dans le processus et le moule, mais l’opérateur et les conditions d’opération influencent le temps de cycle réel atteint. La plupart des compagnies mesurent uniquement le temps de cycle de moulage indirectement et ultérieurement en divisant le temps total pour fabriquer un lot de produits par le nombre de pièces (cycles) produites. Ces données peuvent être utiles pour la comptabilité et l’ingénierie, mais elles soutiennent très peu la gestion du travail et l’amélioration opérationnelle.
La meilleure situation est de continuellement mesurer et afficher le temps de cycle pendant le quart de travail. Ainsi, la direction peut suivre de près le rendement réel de la ressource centrale d’un atelier de moulage, et veiller à ce que l’atelier fonctionne au maximum de sa capacité en temps réel.
De nombreux facteurs déterminent le cycle de moulage réel, dont les actions et les décisions des opérateurs, l’état et l’entretien de l’équipement, et les conditions ambiantes. Une détection précoce de tout inhibiteur de cycle peut mener à des corrections hâtives et à une hausse de la production.
Le design du moule et le processus dictent le temps de cycle de fonctionnement théorique. Cela peut être considéré comme le meilleur cycle global ou le plus optimal. Un fonctionnement plus lent que le cycle optimal théorique représente, bien sûr, une baisse de productivité et d’efficience. Un fonctionnement plus rapide que le cycle prévu n’est pas nécessairement une bonne chose. Par exemple, si le temps de cycle devait être de 11 secondes, mais que le travail réel prend 10 secondes, le produit peut sembler correct dans la machine, mais il pourrait échouer à des tests de qualité par la suite. Une surveillance continue du temps de cycle peut déclencher immédiatement une alerte de qualité exigeant de rapidement vérifier la qualité du produit et de prendre des mesures correctives pour prévenir la production d’autres mauvaises pièces. La plupart du temps, la meilleure pratique est de chercher à atteindre le taux théorique avec constance; ni plus ni moins.
Des machines bien entretenues seront plus rapides et plus fiables, et produiront davantage de rendements constants. L’expérience et l’expertise de l’opérateur peuvent également avoir une incidence importante dans le cycle de moulage et, par conséquent, dans la productivité de la machine et de l’atelier. Posséder un système qui fait le suivi historique du temps de cycle, qui gère les calendriers d’entretien et qui est en mesure d’enregistrer ce que le temps de cycle devrait être par machine est essentiel pour augmenter la productivité globale et la profitabilité de la production tout en offrant des capacités de planification et d’organisation bien meilleures.
Disons qu’un moule est conçu pour un cycle de 10 secondes. Un opérateur moins expérimenté pourrait faire fonctionner la machine à un cycle de 11 secondes afin d’être en mesure d’accomplir ses tâches et de produire de bonnes pièces. Cette seconde supplémentaire de temps de cycle représente une réduction de productivité de 10 %, ce qui signifie qu’une tâche précise prendra 10 % plus de temps à accomplir et que le rendement global de la machine par quart de travail sera réduit de 10 %. Ramener la machine à ses résultats de vitesse prévus est une amélioration de 11 % par rapport au taux réduit (en divisant 9 secondes sur 10 pour obtenir le pourcentage d’amélioration), accompagnée d’une amélioration en efficience et en productivité… Sans oublier la réduction des coûts!
Le suivi du rendement du moulage (temps de cycle) par machine offre également l’occasion de mieux gérer l’atelier et d’atteindre une cadence maximale. Un moule peut fonctionner efficacement à un cycle de 10 secondes sur une machine, mais à 8 secondes sur une autre. Toutes autres choses étant égales, il pourrait être préférable de produire le lot sur la deuxième machine. Le fait de prendre en considération d’autres tâches et leurs taux de fonctionnement, changements de couleur, priorités, calendriers d’entretien, disponibilités des opérateurs et d’autres facteurs peut favoriser des affections alternatives. Ces décisions sont difficiles à prendre sans avoir accès à de bonnes informations sur le rendement qui sont fournies par les données du moule, de la machine et de l’opérateur.
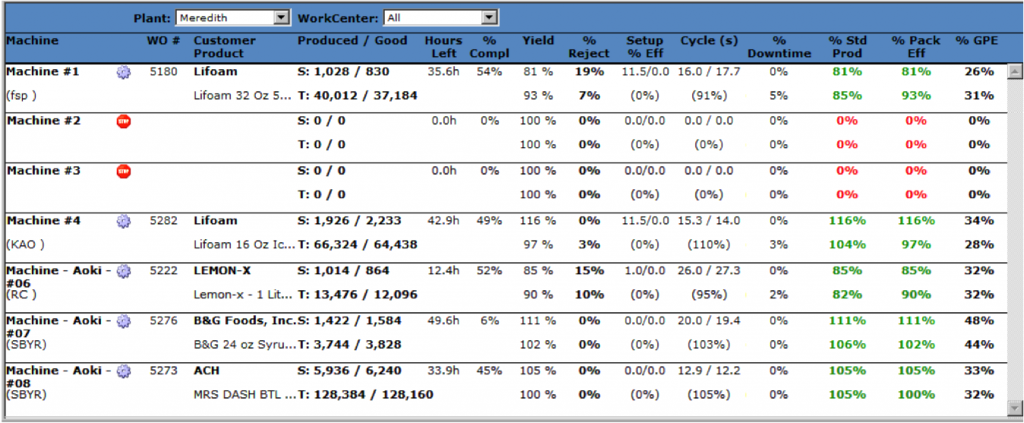
Une autre possibilité est de vérifier constamment le temps de cycle par rapport au rendement du lot. Les données automatisées de l’atelier fournies par la machine, comparées directement aux balayages de code à barres de ce qui est emballé, peuvent évaluer le progrès et la qualité (rejets) du travail. Cela fournit continuellement des données permettant de planifier quand le lot actuel peut être expédié, et quand la production du prochain lot peut démarrer. Le suivi de l’utilisation de matériaux bruts est également plus précis.
Dans la plupart des cas, de simples capteurs de contrôle faisant partie des commandes de la machine (ou pouvant y être ajouté) peuvent être utilisés pour les fonctions de collecte et d’analyse de données dans votre système de planification et de gestion. Un petit investissement dans la collecte de données génère des résultats très précieux pour planifier, opérer et gérer plus efficacement le rendement et l’efficience de l’atelier.